Intralogistics – Virtual warehouse tour with 360° warehouse tour
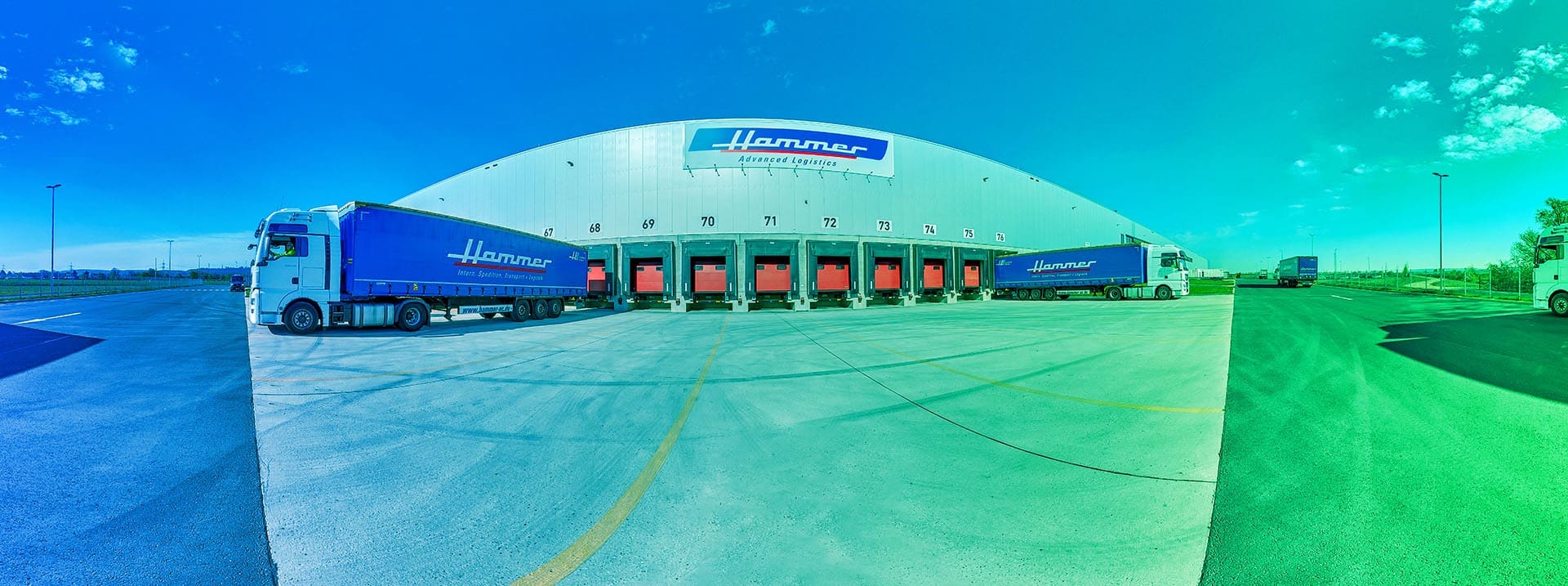
Intralogistics – Virtual warehouse tour
a real 360-degree experienceSie möchten sich schon einmal vorab über die vielseitigen Möglichkeiten des Warehouse Management Systems vom pLG WMS informieren? Kein Problem – mit unserer Intralogistik 360-Grad-Lagerbesichtigung können Sie sich in aller Ruhe durch unser Lager bewegen und einen detaillierten Eindruck unseres WMS pLG WMS gewinnen.
Ein Highlight unserer fortschrittlichen Lösungen ist nämlich die Möglichkeit virtueller Lagerbesichtigungen. Die innovative Technologie ermöglicht es Interessenten und Kunden, unsere Intralogistik-Systeme in Aktion zu sehen, ohne ihr Büro verlassen zu müssen.
Übrigens: Wenn Sie möchten, können Sie sich selbstverständlich auch ohne die Intralogistik 360° virtuelle Lagerbesichtigung ausführlich informieren. Wir haben für alle wichtigen Punkte die wichtigsten Informationen für Sie kurz zusammengefasst. Und wenn Sie trotzdem noch Fragen haben, melden Sie sich einfach bei uns. Wir freuen uns, wenn wir Ihnen weiterhelfen können.
Intralogistics – what sets our approach apart
Our experience in intralogistics is characterized by constant innovation and the deep conviction that every challenge has a solution. Here are some of the pillars of our strategy that position us as a pioneer in the industry:
- Kundenzentrierte Lösungen: Wir entwickeln Systeme, die auf die individuellen Bedürfnisse jedes Lagers zugeschnitten sind, um maximale Effizienz und Produktivität zu gewährleisten.
- Innovative technology: We rely on innovative technologies, such as the KNAPP shuttle system and specially developed software systems. In this way, we ensure that your intralogistics is equipped for the future and meets the increasing requirements.
- Data-driven optimization: We use data analytics to make informed decisions and drive continuous improvement in all aspects of intralogistics.
- Comprehensive integration: Our systems are designed to integrate seamlessly into existing processes, ensuring end-to-end efficiency and consistency.
- Automation for efficiency: We rely on automation to reduce manual errors, increase safety and reduce operating costs.
- Nachhaltige Praktiken: Unsere Lösungen fördern Nachhaltigkeit, indem sie Ressourceneffizienz und umweltfreundliche Praktiken unterstützen.
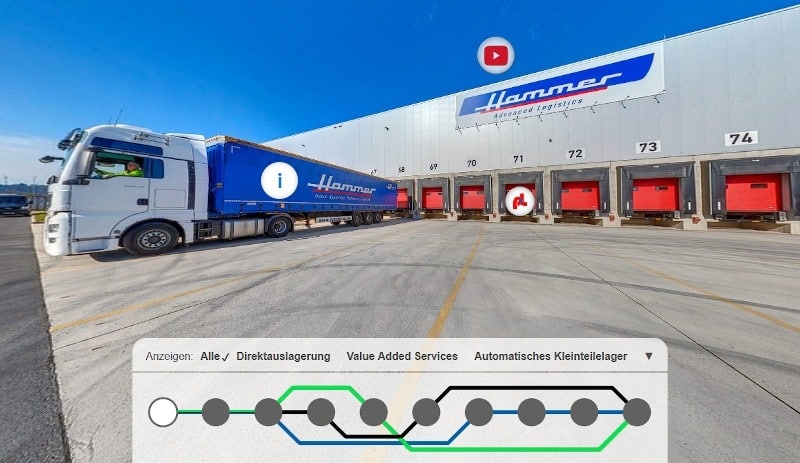
Exterior view of intralogistics warehouse – facts & figures
proLogistik Group
Seit 1983 realisiert proLogistik innovative Soft- und Hardwarelösungen, auch für die Intralogistik. Mehr als 800 Mitarbeiter sind heute, von der Entwicklung, über die Fertigung, bis hin zum Service im Einsatz.
Hammer Group
The Hammer Group is a symbiosis of logistics companies and related industries with its headquarters in Aachen. The Group has access to 350 vehicles, employs 700 people and generates an annual turnover of €135 million.
The range of services is all-encompassing and extends from customized national and European overland transports based on our own state-of-the-art vehicle fleet to air and sea transports with our own bonded warehouse, fully monitored security transports, special silo and bulk goods transports, heavy and plant transports and special Eastern European transports.
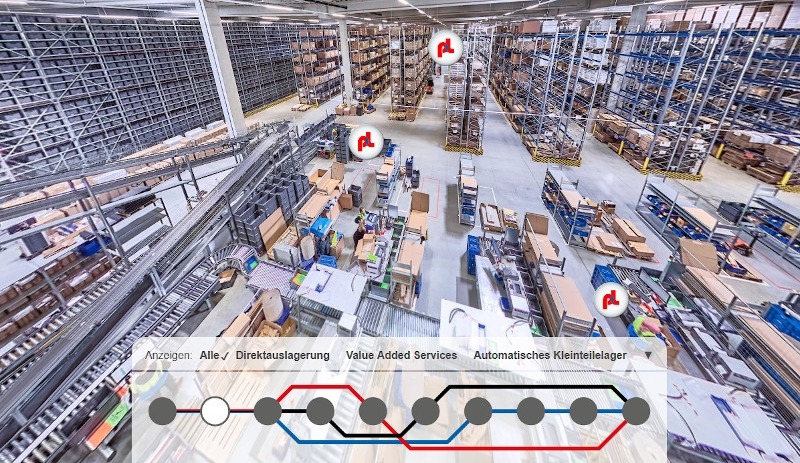
LCE – Logistics Campus Eschweiler
The Eschweiler logistics campus of Hammer GmbH & Co. KG is centrally located on an area of over 105,000 square meters with direct access to the A4 motorway.
- Property: 186,000 square meters
- Usable floor space: 104,000 sqm
- Floor area: 93,489 sqm
- Mezzanine floor: 9,876 sqm
- Offices and social areas: 1,789 sqm
- Employees (planned): 350
proLogistik controls intralogistics with the warehouse management system pLG WMS at the logistics center on the Eschweiler campus. Since then, Hammer has been able to implement any customer requirements on an ongoing basis with complete flexibility.
Essential elements of intralogistics: optimization of processes and technology
The integration of advanced systems and technologies is not only a feature of advanced facilities, but also a key factor for companies wishing to remain competitive in an increasingly competitive market. At proLogistik, we cover the many aspects that are essential for optimizing warehouse and production environments.
- Incoming goods (WE) and outgoing goods (WA): Use of automated systems for fast processing and accurate recording of goods.
- Lagersysteme: Nutzung von Hochregallagern und automatisierten Lagerlösungen, die eine maximale Raumnutzung ermöglichen und die Bestandsverwaltung erleichtern.
- Conveyor systems: Integration of advanced conveyor technologies that ensure a continuous and efficient material flow.
- Picking software and sorting systems: Introduction of advanced picking and sorting systems supported by precise software solutions to minimize errors and speed up order processing.
- Telematics, sensor technology and robotics: Integration of the latest sensor technology and robotics for improved monitoring, automated material handling and preventive maintenance.
- Software for the respective areas: Development and deployment of specialized software solutions that ensure seamless integration and effective management of various processes.
- Complete systems: Providing customized, comprehensive intralogistics systems that cover all aspects from storage to delivery.
Intralogistics of the future
At proLogistik, we believe that the future of intralogistics lies in the further integration of advanced technology, artificial intelligence and sustainable practices. Our commitment to innovation means that we are constantly exploring new ways to increase efficiency, reduce costs and improve warehouse performance.
With our customized solutions, our commitment to customer service and our pioneering role in technological innovation, we are here to help you master your logistics challenges and take your business into the future.
We will be happy to advise you on our products
We are here for you.Give us a call or send us a message. We look forward to welcoming you.
proLogistik Holding GmbH
Fallgatter 1
44369 Dortmund
Tel.: +49 (0) 231 5194-0
Tel.: +41 (0) 44 200 40-00
Tél.: +33 (0) 251 81 85 85
FAQ – Frequently asked questions
Digitalization plays a key role in the evolution of intralogistics. By integrating digital technologies, companies can obtain real-time data about their supply chains, leading to improved decision-making processes, greater efficiency and reduced operating costs. Digitalization also enables the automation of complex processes, improves inventory accuracy, minimizes errors and promotes an agile response to market changes.
AI is a game changer in the world of intralogistics, as it optimizes processes that were previously considered too complex or time-consuming. Through machine learning and data analysis, AI systems can recognize patterns, make predictions and make autonomous decisions that increase efficiency. They improve inventory management, facilitate predictive maintenance, minimize downtime and assist with dynamic route planning, all of which add up to a significant increase in productivity and cost savings.
Intralogistics is crucial for customer satisfaction as it has a direct impact on delivery times, inventory accuracy and order integrity. Optimized warehousing, picking and shipping processes enable companies to ensure fast, reliable and accurate deliveries. This increases customer satisfaction and loyalty. In addition, efficient intralogistics enables a faster response to customer requests and needs, resulting in an improved customer experience and a stronger brand image.